Plastic extrusion specialists delivering precision and quality
Plastic extrusion specialists delivering precision and quality
Blog Article
A Comprehensive Overview to the Process and Advantages of Plastic Extrusion
In the large realm of manufacturing, plastic extrusion becomes a highly reliable and essential procedure. Altering raw plastic into constant profiles, it accommodates a wide variety of industries with its impressive adaptability. This overview aims to clarify the detailed steps included in this technique, the kinds of plastic suitable for extrusion, and the game-changing advantages it offers the sector. The following discussion guarantees to unfold the real-world influences of this transformative process.
Recognizing the Essentials of Plastic Extrusion
While it might show up complicated initially glimpse, the procedure of plastic extrusion is fundamentally easy - plastic extrusion. It is a high-volume manufacturing strategy in which raw plastic is melted and shaped into a continuous profile. The process begins with the feeding of plastic product, in the form of pellets, powders, or granules, right into a heated barrel. The plastic is after that thawed utilizing a mix of warmth and shear, applied by a rotating screw. Once the molten plastic reaches completion of the barrel, it is required with a tiny opening called a die, shaping it into a desired form. The designed plastic is then cooled down, strengthened, and cut right into wanted lengths, completing the process.
The Technical Refine of Plastic Extrusion Explained
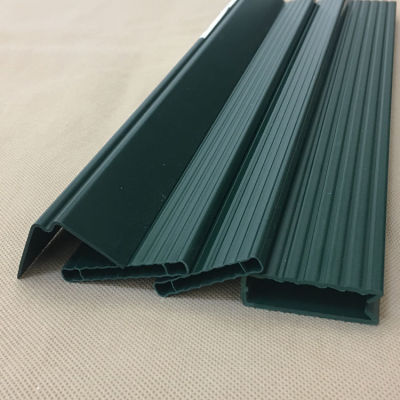
Kinds of Plastic Suitable for Extrusion
The selection of the right kind of plastic is an important element of the extrusion process. Different plastics use one-of-a-kind residential properties, making them much more suited to certain applications. Polyethylene, as an example, is typically used due to its low expense and very easy formability. It provides exceptional resistance to chemicals and wetness, making it perfect for items like tubing and containers. Polypropylene is another prominent selection due to its high melting factor and resistance to fatigue. For more robust applications, polystyrene and PVC (polyvinyl chloride) are typically picked for their stamina and durability. These are typical choices, the choice eventually depends on the particular requirements of the product being generated. Understanding these plastic kinds can substantially boost the extrusion procedure.
Comparing Plastic Extrusion to Various Other Plastic Forming Techniques
Recognizing the sorts of plastic appropriate for extrusion leads the way for a broader conversation on just how plastic extrusion compares to other plastic developing techniques. These include shot molding, impact molding, and thermoforming. Each technique has its distinct usages and advantages. Injection molding, for example, is superb for producing elaborate components, while impact molding is best for basics hollow items like containers. Thermoforming excels at developing superficial or big parts. Plastic extrusion is exceptional when it comes to producing constant profiles, such as gaskets, seals, and pipelines. It additionally permits a consistent cross-section along the length of the item. Hence, the selection of approach mostly relies on the end-product requirements and requirements.
Key Benefits of Plastic Extrusion in Production
In the world of production, plastic extrusion supplies many substantial advantages. One significant advantage is the cost-effectiveness of the procedure, which makes it an economically attractive manufacturing method. In addition, this method offers superior item adaptability and improved production speed, check my site thus raising total manufacturing efficiency.
Cost-Effective Manufacturing Method
Plastic extrusion jumps to the center as an economical manufacturing technique in production. Additionally, plastic extrusion needs less power than standard manufacturing methods, adding to reduced operational expenses. Generally, the economic benefits make plastic extrusion an extremely eye-catching alternative in the production industry.
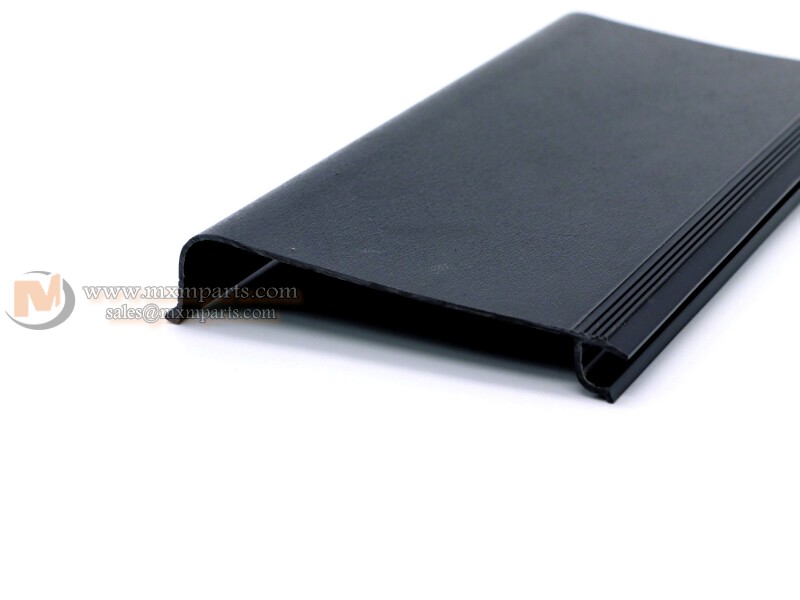
Superior Item Versatility
Past the cost-effectiveness of plastic extrusion, another substantial benefit in making lies in its exceptional product versatility. This makes plastic extrusion a suitable service for industries that require tailored plastic components, such as automotive, building and construction, and packaging. In essence, plastic extrusion's product versatility promotes technology while improving functional effectiveness.
Boosted Production Speed
A significant advantage of plastic extrusion exists in its boosted manufacturing speed. This production procedure permits for high-volume production in a fairly brief time period. It is capable of producing long, continual plastic accounts, which considerably lowers the production time. This high-speed manufacturing is especially beneficial in sectors where huge quantities of plastic components are required within limited target dates. Few other manufacturing processes can match the speed of plastic extrusion. In addition, the capacity to keep regular high-speed production without giving up item high quality establishes plastic extrusion apart from other methods. The enhanced production speed, for that reason, not only allows producers to satisfy high-demand orders but also contributes to boosted effectiveness and cost-effectiveness. This beneficial attribute of plastic extrusion has actually made it a recommended option in numerous sectors.
Real-world Applications and Effects of Plastic Extrusion
In the realm of production, the method of plastic extrusion holds extensive importance. The economic benefit of plastic extrusion, mostly its economical and high-volume output, has actually transformed production. The market is persistently making every effort for technologies in eco-friendly and recyclable materials, indicating a future where the my company benefits of plastic extrusion can be kept without compromising environmental sustainability.
Conclusion
Finally, plastic extrusion is a very reliable and efficient method of changing raw products into varied items. It supplies many advantages over various other plastic creating techniques, including cost-effectiveness, high outcome, very little waste, and design versatility. Its influence is profoundly felt in different sectors such as construction, automobile, and durable goods, making it an essential procedure in today's production landscape.
Delving much deeper right into the technical process of plastic extrusion, it starts with the option of the proper plastic material. As soon as cooled down, the plastic is cut into the called for lengths or wound onto reels if the item is a plastic movie or sheet - plastic extrusion. Comparing Plastic Extrusion to Various Other Plastic Forming Techniques
Understanding the types of plastic ideal for extrusion paves the way for a more comprehensive conversation on how plastic extrusion piles up against other plastic developing approaches. Few various other manufacturing procedures can match the speed of plastic extrusion.
Report this page